3D Printed House Construction BUNDLE BUNDLE
Are you ready to transform your approach to 3D printed house construction? Which 5 KPIs drive cost tracking, material usage, operational uptime, customer satisfaction, and sustainability? Explore dynamic metrics that ignite smart, data-driven decisions.
Curious how financial and operational metrics boost efficiency in building projects? Harness insights from predictive analytics and budget adherence to ensure on-time delivery. Enhance your strategy with our 3D Printed House Construction Business Plan Template for actionable guidance.
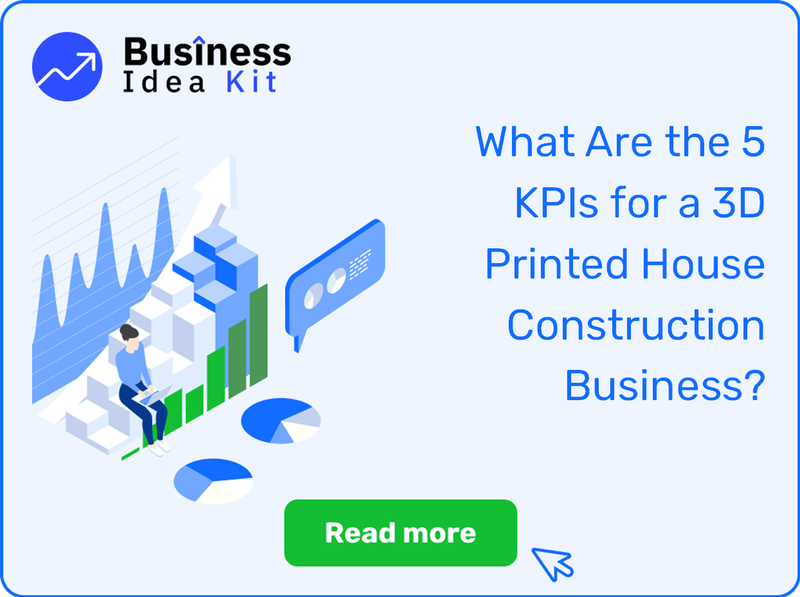
# | KPI Name | Description |
---|---|---|
1 | Average Project Cost | Tracks average spending per project, benchmarked between $150,000 and $300,000, to guide pricing and capital forecasting. |
2 | Construction Time Efficiency | Measures project duration with benchmarks of 60–90 days and aims for 95% on-time completion to enhance ROI. |
3 | Material Usage Efficiency | Assesses material consumption with target wastage below 5% to maximize sustainability and cost control. |
4 | Operational Downtime | Monitors machine uptime above 90%, reducing unplanned downtime to under 10% to optimize project delivery. |
5 | Customer Satisfaction Index | Measures post-project satisfaction with targeted scores above 85% through surveys and referrals to drive continuous improvement. |
Key Takeaways
- Tracking KPIs in 3D printed house construction is crucial for real-time monitoring of costs and project timelines.
- Understanding financial metrics like gross profit margins is essential for ensuring profitability in your projects.
- Operational KPIs can significantly enhance efficiency and reduce costs, driving competitive advantages in the market.
- Focusing on customer-centric KPIs helps improve satisfaction and fosters repeat business, which is vital for long-term success.
Why Do 3D Printed House Construction Need to Track KPIs?
Tracking Key Performance Indicators (KPIs) is essential for the success of your 3D printed house construction business. By focusing on real-time data, you can enhance efficiency and minimize costs, ensuring your projects stay on budget and on schedule. Let’s dive into why these metrics are critical for your operations.
Key Reasons to Track KPIs
- Real-time monitoring of construction costs helps prevent overruns, keeping your budget intact.
- Immediate detection of delays and technical glitches minimizes downtime, enhancing productivity.
- Assessing material usage efficiency promotes sustainable building practices and reduces waste.
- Data-driven forecasting refines project timelines, ensuring you meet your operational goals.
By leveraging these insights, you can significantly improve your 3D printing building efficiency. For more detailed financial metrics, check out How Much Does it Cost to Start Constructing a 3D Printed House?.
What Financial Metrics Determine 3D Printed House Construction’s Profitability?
Understanding the financial metrics that drive profitability is crucial for any 3D printed house construction business. By focusing on key performance indicators (KPIs), you can ensure cost-effectiveness and sustainable growth. Let’s dive into the essential metrics you need to track.
Essential Financial Metrics
- Measure gross and net profit margins per project, aiming for benchmarks between 15%–25%.
- Analyze EBITDA margins, targeting 10%–20% for sustained profitability in the innovative construction sector.
- Track prime costs, such as material and labor expenses, which typically constitute 30%–50% of total project costs.
- Evaluate break-even points, which may occur within 2–3 years based on initial investments and operational efficiencies.
- Monitor cash flow cycles to align funding with project milestones and technology upgrades.
For more insights on the financial aspects, check out How Much Does it Cost to Start Constructing a 3D Printed House?.
How Can Operational KPIs Improve 3D Printed House Construction Efficiency?
Operational KPIs are crucial for enhancing efficiency in 3D printed house construction. By focusing on key metrics, you can significantly streamline processes, reduce costs, and improve overall project outcomes. Let's explore how these KPIs can transform your construction operations.
Key Operational KPIs for Efficiency
- Analyze print speed and accuracy to ensure quality control, aiming for error rates below 5% per project phase.
- Monitor machine uptime versus downtime, targeting an operational uptime above 90%.
- Assess material consumption per unit area to benchmark against traditional methods, typically within a 10%–15% cost variation margin.
- Review maintenance efficiency to limit disruptions, ensuring smooth construction processes.
For further insights on tracking these KPIs, check out 3D Printing Business KPI Metrics.
Additionally, understanding the financial aspect is vital. Explore How Much Does a 3D Printed House Construction Owner Earn? to gain insights into potential earnings in this innovative sector.
What Customer-Centric KPIs Should 3D Printed House Construction Focus On?
In the rapidly evolving world of 3D printed house construction, understanding customer-centric KPIs is vital for driving success and ensuring sustainability. By focusing on key performance indicators that reflect customer satisfaction and engagement, you can enhance your service offerings and build a loyal client base. Let's dive into the essential metrics you should be tracking.
Key Customer-Centric KPIs
- Track customer satisfaction ratings post-construction, aiming for over 85% positive feedback.
- Monitor customer acquisition cost (CAC) to remain below 15% of project value for profitability.
- Evaluate repeat engagement and referral rates, targeting a 20%–30% return customer base.
- Measure Net Promoter Score (NPS) with benchmarks above 50 to gauge loyalty and market perception.
By focusing on these 3D printing construction KPIs, you can ensure that your business remains competitive and responsive to customer needs. For more insights, check out Industry Insight: 3D Printing Rapid Prototyping Services. Additionally, if you're curious about the financial aspects, learn How Much Does it Cost to Start Constructing a 3D Printed House?.
How Can 3D Printed House Construction Use KPIs to Make Better Business Decisions?
Harnessing KPIs in 3D printed house construction is essential for making informed business decisions that drive growth and efficiency. By integrating these metrics into your strategy, you can ensure a balance between innovation and financial stability. Let’s explore how you can leverage these insights for impactful outcomes.
Key Actions for Better Decision-Making
- Integrate KPI metrics with long-term growth strategies for a balanced approach.
- Utilize predictive analytics to project a 15%–25% improvement in efficiency over multiple years.
- Implement real-time tracking of production costs to reduce overhead by approximately 10%.
- Combine operational data with customer feedback to refine service offerings and enhance project outcomes.
For more insights on how to track KPIs in 3D printed house construction, check out data-driven insights for 3D printed house construction.
Additionally, understanding how much it costs to start constructing a 3D printed house can further guide your financial planning and operational decisions.
What Are 5 Core KPIs Every 3D Printed House Construction Should Track?
KPI 1: Average Project Cost
Definition
The Average Project Cost measures the typical expenditure incurred for each construction project within the 3D printed house construction sector. This KPI is crucial for evaluating financial performance and guiding pricing strategies, ensuring that your projects remain profitable while meeting market demands.
Advantages
- Helps in setting competitive pricing strategies based on real market data.
- Facilitates better budgeting and financial forecasting for future projects.
- Enables identification of cost overruns and areas for operational improvement.
Disadvantages
- May not account for external factors like market fluctuations and material costs.
- Can lead to misinterpretation if not compared against industry benchmarks.
- Requires accurate data collection, which can be resource-intensive.
Industry Benchmarks
In the 3D printed house construction industry, the Average Project Cost typically ranges from $150,000 to $300,000 per unit. These benchmarks are essential for assessing your business's performance against competitors and ensuring that your pricing strategies align with market expectations.
How To Improve
- Implement detailed cost tracking systems to monitor expenditures in real-time.
- Regularly review and adjust project estimates based on historical data.
- Negotiate better rates with suppliers to reduce material costs.
How To Calculate
To calculate the Average Project Cost, use the following formula:
Example of Calculation
For instance, if your total project costs for five homes amount to $1,200,000, the calculation would be:
This means the average cost per project is $240,000, which falls within the industry benchmark.
Tips and Tricks
- Utilize digital construction monitoring tools for accurate cost tracking.
- Regularly update your cost estimates based on current market conditions.
- Analyze past projects to identify patterns in cost overruns.
- Consider using predictive analytics to forecast future project costs.
KPI 2: Construction Time Efficiency
Definition
Construction Time Efficiency measures the total days required to complete a project, focusing on reducing traditional timelines from over 120 days to as low as 60–90 days using advanced 3D printing technology. This KPI is crucial for evaluating the speed and effectiveness of the construction process, directly impacting overall project costs and customer satisfaction.
Advantages
- Enables faster project delivery, enhancing client satisfaction and competitive edge.
- Improves resource allocation by identifying bottlenecks in the construction process.
- Supports ROI calculations by correlating time savings with reduced costs, maximizing profitability.
Disadvantages
- May overlook quality issues if speed is prioritized over craftsmanship.
- Potential for misinterpretation of data if not contextualized with project complexities.
- Requires consistent tracking and updates, which can be resource-intensive.
Industry Benchmarks
In the 3D printed house construction sector, achieving a project completion time of 60–90 days is considered a benchmark for efficiency. This standard is essential for assessing performance against traditional construction methods, which often exceed 120 days. Meeting these benchmarks can significantly enhance market competitiveness.
How To Improve
- Implement automated scheduling tools to streamline project timelines.
- Conduct regular training for staff on efficient 3D printing techniques.
- Utilize predictive analytics to anticipate delays and adjust plans proactively.
How To Calculate
To calculate Construction Time Efficiency, track the total days taken for project completion and compare it to the planned duration. The formula is:
Example of Calculation
For instance, if a project was planned for 75 days but took 90 days to complete, the calculation would be:
This indicates a 20% delay compared to the planned schedule, highlighting areas for improvement.
Tips and Tricks
- Regularly review project timelines to identify and address delays promptly.
- Incorporate feedback loops from team members to enhance process efficiency.
- Utilize digital construction monitoring tools for real-time updates on progress.
- Benchmark against industry standards to set realistic project timelines.
KPI 3: Material Usage Efficiency
Definition
Material Usage Efficiency measures the ratio of actual material consumption against initial estimates in 3D printed house construction. This KPI plays a crucial role in evaluating sustainability and cost control, ensuring that waste levels remain below 5% per project.
Advantages
- Improves sustainability by minimizing waste, aligning with environmental goals.
- Enhances cost control through precise material tracking, reducing over-ordering.
- Facilitates continuous improvement by comparing efficiency metrics across projects.
Disadvantages
- May require sophisticated tracking systems, increasing initial setup costs.
- Potential for misinterpretation if not contextualized with project specifics.
- Can overlook qualitative factors affecting material usage, such as design changes.
Industry Benchmarks
In the 3D printed house construction sector, industry benchmarks for material usage efficiency typically aim for wastage levels below 5%. This standard is essential for assessing performance and ensuring cost competitiveness, especially as the market evolves towards more sustainable practices.
How To Improve
- Implement advanced tracking systems to monitor real-time material usage.
- Conduct regular audits to identify and eliminate wasteful practices.
- Enhance training for staff on efficient material handling and usage.
How To Calculate
To calculate Material Usage Efficiency, use the following formula:
Example of Calculation
For instance, if a project estimated 1,000 kg of material but used 950 kg, the calculation would be:
This indicates efficient material usage, well within the target wastage levels.
Tips and Tricks
- Utilize digital construction monitoring tools for accurate tracking.
- Incorporate predictive analytics to forecast material needs more accurately.
- Engage in continuous training for teams on best practices in material efficiency.
- Regularly review and adjust estimates based on past project data.
KPI 4: Operational Downtime
Definition
Operational downtime refers to the period when machinery is not operational, impacting overall productivity in 3D printed house construction. Tracking this KPI is crucial for maintaining efficiency and ensuring timely project delivery.
Advantages
- Improves project delivery by maintaining operational performance above 90%.
- Reduces costs associated with unplanned downtime, targeting levels below 10%.
- Enhances equipment reliability, leading to more efficient construction processes.
Disadvantages
- May not account for all indirect costs associated with downtime.
- Requires accurate data collection, which can be resource-intensive.
- Potential for misinterpretation if not analyzed in conjunction with other KPIs.
Industry Benchmarks
In the 3D printed house construction industry, maintaining operational uptime above 90% is considered a standard benchmark. This level of efficiency is vital for ensuring that projects are completed on time and within budget, ultimately enhancing profitability.
How To Improve
- Implement predictive maintenance strategies to anticipate equipment failures.
- Regularly schedule maintenance to minimize unexpected downtime.
- Utilize real-time data insights to monitor machine performance and adjust operations accordingly.
How To Calculate
To calculate operational downtime, use the following formula:
Example of Calculation
For instance, if a machine has a total operating time of 1,000 hours and experiences 50 hours of downtime, the calculation would be:
This indicates that the operational downtime is within the acceptable range, supporting efficient project delivery.
Tips and Tricks
- Regularly review maintenance logs to identify patterns in downtime.
- Train staff on efficient machine operation to minimize user-related downtime.
- Invest in advanced 3D printing technology to enhance reliability and reduce failures.
- Utilize predictive analytics to forecast potential issues before they arise.
KPI 5: Customer Satisfaction Index
Definition
The Customer Satisfaction Index measures how satisfied customers are with their experience after a project is completed. This KPI is crucial for understanding client perceptions and improving service quality, which can lead to increased repeat business and referrals.
Advantages
- Enhances customer loyalty by identifying areas for improvement.
- Informs marketing strategies by understanding customer preferences.
- Drives operational improvements through actionable feedback.
Disadvantages
- May not capture the full customer experience if surveys are not comprehensive.
- Can be influenced by external factors unrelated to service quality.
- Requires consistent tracking to be meaningful, which can be resource-intensive.
Industry Benchmarks
In the 3D printed house construction sector, a customer satisfaction score above 85% is considered excellent. This benchmark is vital for evaluating your performance against competitors and ensuring that your services meet or exceed industry standards.
How To Improve
- Implement regular customer feedback surveys to gather insights.
- Train staff on customer service best practices to enhance interactions.
- Analyze feedback to identify trends and areas needing improvement.
How To Calculate
To calculate the Customer Satisfaction Index, use the formula:
Example of Calculation
Suppose you received 200 survey responses, with 170 indicating satisfaction. The calculation would be:
This score indicates you meet the industry benchmark for customer satisfaction.
Tips and Tricks
- Utilize digital tools for real-time feedback collection.
- Encourage customers to leave online reviews to enhance visibility.
- Regularly benchmark against competitors to stay competitive.
- Incorporate feedback into training programs for continuous improvement.