3D Printed House Construction BUNDLE BUNDLE
Have you ever wondered how much it costs to start constructing a 3D printed house? With innovative construction techniques and variable material expenses, the journey is both exciting and unpredictable. Are you prepared to explore every cost detail?
Curious about startup expenses, from equipment to regulatory fees? Our guide unravels the comprehensive cost factors impacting 3D printed house startup costs. Discover the insights within our 3D Printed House Construction Business Plan Template and sharpen your financial strategy.
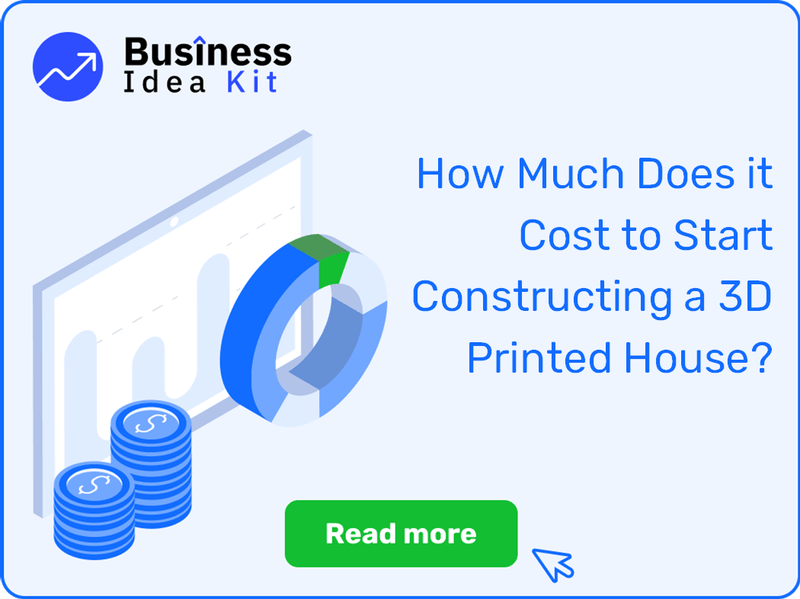
# | Startup Cost | Description | Min Amount | Max Amount |
---|---|---|---|---|
BuildTech Innovations revolutionizes residential construction through advanced 3D printing technology, offering faster, more affordable, and sustainable housing solutions. The company combines cutting-edge technology with environmental responsibility to address the growing demand for innovative housing while establishing multiple revenue streams through direct sales and technology licensing. startup costs. |
||||
1 |
Real Estate & Land Preparation |
Costs for land acquisition, site stabilization, surveys, and utility connection deposits. |
$30,000 - $30,000 |
$100,000 - $100,000 |
2 |
3D Printing Equipment |
Investment in advanced machinery, maintenance contracts, software licenses, and custom upgrades. |
$200,000 - $200,000 |
$1,000,000 - $1,000,000 |
3 |
Construction Materials |
Procurement of specialized polymers, composites, quality assurance testing, and logistics management. |
$50,000 - $50,000 |
$150,000 - $150,000 |
4 |
Design & Engineering Software |
Fees for architectural design, engineering consultations, custom software development, and iterative prototyping. |
$45,000 - $45,000 |
$190,000 - $190,000 |
5 |
Permits & Insurance |
Expenses covering permit fees, regulatory assessments, insurance premiums, and legal consultations. |
$5,000 - $5,000 |
$20,000 - $20,000 |
6 |
Labor & Training |
Recruitment, onboarding, specialized staffing, and comprehensive training programs. |
$50,000 - $50,000 |
$150,000 - $150,000 |
7 |
Marketing & Business Development |
Allocation for initial marketing campaigns, digital presence development, and strategic advertising initiatives. |
$25,000 - $25,000 |
$65,000 - $65,000 |
Total |
$405,000 |
$1,675,000 |
Key Takeaways
- Startup costs for a 3D printed house construction business can range from $405,000 to $1,675,000.
- Material quality and technological complexity are significant factors that can increase costs by 10%–25%.
- Labor expenses, including staff salaries and training, can represent up to 35%–40% of ongoing operational costs.
- It’s essential to establish a contingency fund of 10%–15% to prepare for hidden and unexpected expenses.
What Are Main Factors That Influence 3D Printed House Construction Startup Costs?
Understanding the factors that impact startup costs for 3D printed house construction is crucial for your financial planning. Each element can significantly affect your budget, so let’s break down the key considerations that will shape your expenses.
Main Cost Influencers
- Material quality and choice can increase expenses by 15%–25%.
- Technological complexity may add an extra 10%–20% in initial outlay.
- Location-specific regulations could elevate costs by around 7%–15%.
- Supply chain logistics and material availability can influence prices by up to 30%.
Additionally, customization requests and ongoing R&D investments will further impact your overall budget. For a comprehensive guide, check out How to Start a 3D Printed House Construction Business Successfully?. By understanding these 3D construction cost factors, you can better manage your budget for your 3D printed house startup costs.
What Are Biggest One-Time Expenses When Opening 3D Printed House Construction?
Understanding the biggest one-time expenses in 3D printed house construction is crucial for effective budgeting. These costs can significantly impact your overall startup strategy, so let’s break them down to ensure you’re prepared.
Key One-Time Expenses
- Acquisition of specialized 3D printing equipment can represent 40%–60% of startup expenses.
- Land acquisition and site stabilization expenses may range between 20%–30% of total costs.
- Infrastructure modification and utility installations can require an investment of $50,000 or more.
- Professional design, engineering consultations, and software licensing range from $20,000 to $50,000.
- Permits, inspections, and regulatory fees can be up to 10% of the overall budget.
- Initial quality control, finishing work, and post-production enhancements demand additional capital.
- Launch marketing and brand development often require a dedicated budget allocation to generate awareness.
To dive deeper into managing your budget for 3D printed house construction, consider exploring What Are the 5 Key Performance Indicators and Metrics for a 3D Printed House Construction Business? for valuable insights.
What Are Ongoing Monthly Costs of Running 3D Printed House Construction?
Understanding the ongoing monthly costs of running a 3D printed house construction business is crucial for maintaining financial health and sustainability. These costs can significantly impact your budget and profitability. Let’s break down the essential expenses you need to consider.
Key Ongoing Costs
- Operational energy expenses can account for 8%–12% of monthly budgets.
- Regular maintenance and servicing of 3D printing equipment are essential, typically calculated as an 8% annual cost divided monthly.
- Skilled technician and engineering staff salaries usually represent 35%–40% of ongoing expenses.
- Land lease or financing repayments may contribute 25%–35% to recurring budgets.
- Consumable materials and replacement supplies should be budgeted to reflect a 10%–15% monthly increment.
- Software subscription and system upgrade fees can steadily add to operational costs.
For further operational insights, refer to 3D Printed House Insights. Understanding these 3D printed house startup costs will help you manage your budget effectively and prepare for the financial demands of 3D printed house construction.
How Can You Prepare for Hidden and Unexpected Expenses?
In the realm of 3D printed house construction, anticipating hidden costs is crucial for maintaining your budget. By preparing for unexpected expenses, you can ensure smoother project execution. Let’s explore practical strategies to safeguard your finances.
Strategies for Financial Preparedness
- Establish a contingency fund representing 10%–15% of the overall project cost.
- Anticipate emergency repairs, which may range from $5,000 to $20,000 per incident.
- Factor in potential delays in material supply that could increase expenses by roughly 8%–12%.
- Monitor changing regulatory landscapes that might require additional permit renewals and fees.
Additionally, allocate funds for unexpected technological upgrades or system overhauls. Scheduling periodic equipment recalibrations and preventive maintenance budgeting an extra 5%–7% can also prove beneficial. For a detailed cost overview, see Cost Breakdown for 3D Printed Houses. If you want to dive deeper into performance metrics, check out What Are the 5 Key Performance Indicators and Metrics for a 3D Printed House Construction Business?.
What Are Common Pitfalls When Estimating 3D Printed House Construction Startup Costs?
Understanding the common pitfalls in estimating 3D printed house construction startup costs is vital for your success. These miscalculations can lead to significant financial strain and project delays. Let's explore the key areas where many entrepreneurs stumble.
Key Pitfalls to Avoid
- Underestimating material and labor cost fluctuations can lead to budget overruns of 15%–25%.
- Overlooking hidden fees, such as expedited permits or tailored utility setup charges, may increase expenses unexpectedly.
- Relying on optimistic technology ROI projections can result in underfunding for necessary innovations.
- Failing to account for market volatility might cause a 10%–20% deviation from your initial estimates.
- Neglecting scalable software solutions can necessitate future costly upgrades.
- Inadequate contingency planning often results in extra financial strain during unforeseen circumstances.
For more insights on managing your budget for 3D printed house startup costs, consult Pricing Analysis on 3D Printed Houses and learn how to avoid common pitfalls. Additionally, consider checking How to Start a 3D Printed House Construction Business Successfully? for a comprehensive approach.
What Are 3D Printed House Construction Startup Costs?
Startup Cost 1: Real Estate & Land Preparation
Understanding the costs associated with real estate and land preparation is crucial for your 3D printed house construction venture. This expense typically consumes 20%–40% of your startup funds, making it a significant factor in your overall budget. As you navigate this innovative construction landscape, be prepared for industry-specific challenges, such as zoning regulations and site stabilization requirements.
Primary Cost Drivers
The primary cost drivers for real estate and land preparation include land acquisition, site stabilization, and necessary utility connections. These elements can significantly impact your initial investment and should be carefully planned.
Factors Affecting Cost
- Land acquisition costs, which can vary widely based on location
- Site preparation expenses, including clearance and foundation work
- Environmental assessments and zoning verifications
- Utility connection deposits and service fees
Potential Cost Savings
Implementing cost-saving strategies in real estate and land preparation can significantly enhance your budget. Consider bulk purchasing agreements for land and negotiating utility fees to maximize savings.
- Negotiate land prices with sellers
- Utilize local resources for site preparation
- Explore grants for environmental assessments
- Collaborate with utility companies for reduced fees
- Consider alternative sites with lower acquisition costs
- Plan for multi-use land to reduce overall expenses
- Engage in community partnerships for shared resources
- Monitor local market trends for optimal timing
Cost Breakdown for Real Estate & Land Preparation
Expense Component | Estimated Cost | Notes |
---|---|---|
Land Acquisition | $30,000 - $100,000 | Costs vary by location and market conditions |
Site Stabilization & Clearance | $30,000 - $100,000 | Includes foundation work and preparation |
Utility Connection Deposits | Varies | Critical early expenses for service activation |
Environmental Assessments | 5% of total costs | Mandatory for compliance with regulations |
Startup Cost 2: 3D Printing Equipment & Technology Investments
Investing in 3D printing equipment is a critical step for your
Primary Cost Drivers
The primary cost drivers associated with 3D printing equipment include the initial purchase price of advanced machinery, ongoing maintenance contracts, and software integration fees. These factors collectively shape your budget and operational capabilities.
Factors Affecting Cost
- Type and sophistication of 3D printing machinery
- Annual maintenance contracts, typically 8%–10% of equipment value
- Initial software licenses and technology integration fees
- Custom modifications and upgrades, potentially increasing costs by 15%
Potential Cost Savings
To optimize your investment in 3D printing technology, consider strategies that can lead to significant cost savings. By leveraging bulk purchasing and exploring financing options, you can reduce initial expenses and enhance your return on investment.
- Negotiate bulk purchase discounts on equipment
- Explore financing options to spread out costs
- Utilize open-source software to minimize licensing fees
- Invest in training to reduce maintenance costs
- Regularly review equipment performance to avoid unnecessary upgrades
- Implement preventive maintenance to extend equipment lifespan
- Consider leasing options for high-cost machinery
- Engage in partnerships for shared technology resources
3D Printing Equipment Cost Breakdown
Expense Component | Estimated Cost | Notes |
---|---|---|
Advanced 3D Printing Machinery | $200,000 - $1,000,000 | Initial investment for high-quality equipment |
Annual Maintenance Contracts | $16,000 - $100,000 | 8%–10% of equipment value, divided monthly |
Software Licenses & Integration | $20,000 - $50,000 | Initial fees for necessary software |
Custom Modifications | +15% of equipment cost | Potential additional costs for tailored upgrades |
Startup Cost 3: Construction Materials & Supplies
When embarking on 3D printed house construction, understanding the costs associated with construction materials and supplies is vital. This expense typically constitutes 10%–20% of your overall startup costs, making it a significant factor in your budget. As you navigate this innovative construction landscape, be prepared for fluctuations in material prices and the need for high-quality components to ensure durability and compliance with 3D printed building regulations.
Key Cost Drivers
The primary cost drivers for construction materials include the quality of polymers and composites, which directly impact the structural integrity of the 3D printed houses. Additionally, logistics and storage considerations can significantly affect your overall material expenses.
Factors Affecting Cost
- Material quality and choice can increase costs by 10%–20%.
- Price fluctuations can impact overall expenses by as much as 12% annually.
- Bulk purchasing discounts may reduce per-unit costs by 5%–10%.
- Quality assurance and testing add approximately 3% extra to material expenses.
Potential Cost Savings
Implementing cost-saving strategies can help manage your budget for construction materials effectively. By exploring bulk purchasing options and optimizing logistics, you can significantly reduce your overall material costs.
- Negotiate bulk purchasing agreements with suppliers.
- Utilize local suppliers to minimize shipping costs.
- Implement just-in-time inventory practices to reduce storage expenses.
- Invest in quality assurance processes to avoid costly reworks.
- Explore alternative materials that meet regulatory standards.
- Leverage technology for efficient supply chain management.
- Regularly review and adjust your material sourcing strategy.
- Consider partnerships with material manufacturers for discounts.
Construction Materials Cost Breakdown
Expense Component | Estimated Cost | Notes |
---|---|---|
Specialized Polymers | $50,000 - $150,000 | High-quality materials essential for structural integrity. |
Logistics & Storage | $5,000 - $20,000 | Costs related to transportation and warehousing. |
Quality Assurance Testing | $3,000 - $10,000 | Ensures compliance with safety and durability standards. |
Startup Cost 4: Design, Engineering & Software
Design, engineering, and software costs are critical components of your 3D printed house construction venture. These expenses can significantly impact your overall startup budget, ranging from $30,000 to $150,000 based on complexity. Understanding these costs is essential for accurate financial planning and successful project execution.
Cost Drivers
The primary cost drivers in this category include architectural design fees, engineering consultations, and custom software development. Each of these elements is vital for ensuring that your 3D printed house meets both aesthetic and structural standards.
Factors Affecting Cost
- Complexity of architectural and structural designs
- Hourly rates for engineering consultations
- Custom software development and integration needs
- Iterative design prototyping requirements
Potential Cost Savings
Implementing cost-saving strategies can help manage your design, engineering, and software expenses effectively. By leveraging existing software solutions and optimizing design processes, you can reduce overall costs.
- Utilize open-source software for design
- Negotiate hourly rates with engineering consultants
- Adopt modular design approaches to minimize changes
- Invest in training for in-house design capabilities
- Explore partnerships with universities for design support
- Implement feedback loops to reduce prototyping iterations
- Leverage cloud-based solutions for software management
- Conduct thorough market research to inform design choices
Cost Breakdown for Design, Engineering & Software
Expense Component | Estimated Cost | Notes |
---|---|---|
Architectural Design Fees | $30,000 - $150,000 | Based on complexity and scope of the project |
Engineering Consultations | $100 - $200 per hour | Varies by expertise and project requirements |
Custom Software Development | $15,000 - $40,000 | Includes integration and licensing fees |
Iterative Prototyping Costs | +10% - 15% of design costs | For adjustments and refinements |
Startup Cost 5: Permits, Regulatory Approvals & Insurance
Understanding the costs associated with permits, regulatory approvals, and insurance is essential for your 3D printed house construction venture. These expenses can significantly impact your overall budget, often ranging from $5,000 to $20,000 depending on your location and project scope. Navigating the regulatory landscape can be complex, making it crucial to account for these costs early in your planning process.
Cost Drivers
The primary cost drivers in this category include permit and inspection fees, mandatory regulatory assessments, and insurance premiums. Each of these components can add a substantial amount to your overall startup costs, making it vital to budget accordingly.
Factors Affecting Cost
- Permit and inspection fees can vary significantly based on local regulations.
- Mandatory regulatory assessments may add an additional 5%–7% to your total costs.
- Insurance premiums for liability and construction risks typically increase costs by 3%–8%.
- Legal consultation fees can average between $100 and $300 per hour.
Potential Cost Savings
Implementing effective cost-saving strategies can help mitigate expenses related to permits and insurance. By planning ahead and leveraging local resources, you can reduce your overall financial burden.
- Utilize online resources for permit applications to save on legal fees.
- Engage with local building departments early to clarify requirements.
- Consider bundling insurance policies for discounts.
- Stay updated on regulatory changes to avoid unexpected fees.
- Network with other builders to share insights on cost-effective practices.
- Invest in compliance training for staff to reduce legal consultation needs.
- Review and negotiate insurance premiums annually.
- Establish a contingency fund for unexpected regulatory costs.
Cost Breakdown for Permits and Insurance
Expense Component | Estimated Cost | Notes |
---|---|---|
Permit Fees | $5,000 - $20,000 | Varies by location and project scope. |
Regulatory Assessments | 5% - 7% of total costs | Mandatory for compliance. |
Insurance Premiums | 3% - 8% of project costs | For liability and construction risks. |
Legal Consultation Fees | $100 - $300 per hour | Average rates for legal advice. |
Startup Cost 6: Labor, Staffing & Training
Labor, staffing, and training expenses are critical components of your 3D printed house construction startup costs. These costs can significantly impact your budget, often consuming 25%–35% of overall labor expenses. As you build your team, understanding these costs will help you manage your resources effectively and ensure you have the right expertise to drive your business forward.
Cost Drivers
The primary cost drivers for labor and training include recruitment of specialized staff, comprehensive training programs, and the current labor market conditions. Each of these factors can lead to substantial variations in your overall expenses.
Factors Affecting Cost
- Recruitment of specialized technical staff and engineers
- Comprehensive training programs and certification courses
- Skilled labor market conditions driving wage inflation
- Initial onboarding costs that can delay project timelines
Potential Cost Savings
Implementing cost-saving strategies can help you manage your labor and training expenses effectively. Consider optimizing your recruitment process and investing in employee retention to reduce turnover costs.
- Utilize online platforms for efficient recruitment
- Offer in-house training to reduce external training costs
- Implement flexible work arrangements to attract talent
- Develop a mentorship program to enhance staff skills
- Leverage internships for cost-effective staffing solutions
- Negotiate bulk training course rates with providers
- Encourage cross-training to maximize staff versatility
- Monitor industry salary trends to stay competitive
Labor and Training Cost Breakdown
Expense Component | Estimated Cost | Notes |
---|---|---|
Recruitment Costs | $50,000 - $150,000 | Includes hiring specialized staff and engineers |
Training Programs | $10,000 - $30,000 | Comprehensive training and certification courses |
Onboarding Costs | Variable | Can delay project timelines if not budgeted |
Startup Cost 7: Marketing, Sales & Business Development
Marketing is a critical component in launching your 3D printed house construction venture. Allocating between $20,000 and $50,000 for initial marketing campaigns ensures that you effectively reach your target audience and establish a strong brand presence. In a competitive landscape, a well-planned marketing strategy can significantly enhance customer acquisition and overall business growth.
Primary Cost Drivers
The main cost drivers in marketing for a 3D printed house construction business include digital presence development, advertising expenses, and promotional campaigns. Each of these elements plays a vital role in attracting potential customers and generating leads.
Factors Affecting Cost
- Initial marketing campaign allocation
- Website development costs
- Local and digital advertising strategies
- Customer acquisition costs (CPA)
Potential Cost Savings
Implementing cost-saving strategies can help optimize your marketing budget. Focusing on targeted advertising and leveraging social media can lead to significant savings while maximizing outreach.
- Utilize social media platforms for organic reach
- Negotiate bulk rates with advertising agencies
- Implement referral programs to reduce CPA
- Leverage content marketing to enhance visibility
- Monitor analytics to refine strategies
- Collaborate with influencers for cost-effective promotions
- Use email marketing to engage existing leads
- Focus on local partnerships to reduce costs
Cost Breakdown for Marketing, Sales & Business Development
Expense Component | Estimated Cost | Notes |
---|---|---|
Initial Marketing Campaigns | $20,000 - $50,000 | Includes promotional efforts and outreach strategies. |
Digital Presence Development | $5,000 - $15,000 | Covers website creation and online branding. |
Advertising Costs | $10,000 - $30,000 | Local and digital advertising initiatives. |
Customer Acquisition Costs | $50 - $150 per lead | Measured CPA based on marketing effectiveness. |